O Mapeamento de Fluxo de Valor é uma ferramenta que ajuda a identificar o fluxo de material e informação dentro de uma organização. Para desenvolver, deve-se apenas seguir a trilha da produção de um produto, desde o consumidor até o fornecedor, e, cuidadosamente desenhar uma representação visual de cada processo no fluxo de material e informação. Normalmente o Mapa de Fluxo de Valor é feito em uma única página e mostra desde o recebimento da ordem de serviço até a entrega do produto final.

Mapeamento do Fluxo de Valor - VSM
O Lean Manufacturing é uma filosofia que busca eliminar desperdícios, ou seja, excluir o que não tem valor para o cliente e imprimir velocidade à empresa. As origens do Lean Manufacturing vem do Sistema Toyota de Produção. Taiichi Ohno, um executivo da Toyota, iniciou, na década de 1950, a criação e implementação de um sistema de produção cujo principal foco era a identificação e a eliminação de desperdícios, com o objetivo de reduzir custos e aumentar a qualidade e a velocidade de entrega do produto aos clientes. O Sistema Toyota de Produção foi denominado produção enxuta (Lean Production ou Lean Manufacturing) por James P. Womack e Daniel T. Jone, no livro A Máquina que Mudou o Mundo. O livro foi publicado em 1990 nos Estados Unidos com o título original The Machine that Changed the World, é um estudo sobre a indústria automobilística mundial realizado na década de 1980 pelo Massachusetts Institute of Technology (MIT), que chamou a atenção de empresas de diversos setores e vem sendo aplicado nos mais diversos seguimentos industriais.
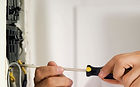
Manutenção Produtiva Total - TPM
O TPM tem por objetivo a capacitação e envolvimento dos operadores no equipamento, com o propósito de atingir o máximo de Eficiência dos Equipamentos, promover melhorias no seu ambiente de trabalho e garantir o nível de produtividade e qualidade sem desperdícios. O TPM busca a máxima eficiência dos sistemas produtivos visando a eliminação total das perdas, aumentando o ciclo total de vida útil dos equipamentos, envolvendo todos os funcionas com foco na quebra zero dos recursos produtivos.
O papel do 5S é cuidar da base, facilitando o aprendizado e prática de conceitos e ferramentas para a qualidade. Isso inclui cuidar dos ambiente, equipamentos, materiais, métodos, medidas, e, especialmente, pessoas.
5S representa cinco palavras japonesas que começam com a letra S:
Seiri - Senso de Utilização
Seiton - Senso de Ordenação
Seisou - Senso de Limpeza
Seiketsu - Senso de Saúde
Shitsuke -Senso de Autodisciplina

Gestão Visual
É a gestão por meio da visualização do status das atividades em andamento, por parte dos gestores e dos colaboradores, permitindo acompanhamento da produção e tomadas de ações, quando necessárias.
O Andon é uma importante ferramenta de gestão visual para identificar quando as anormalidades ocorrem. Vem da palavra japonesa "lâmpada". Normalmente são luzes em máquinas ou linhas de produção que indicam o estado da operação. A corda do andon deve ser puxada para interromper o processo e garantir a qualidade.

Trabalho Padronizado
É a ferramenta usada no Lean Manufacturing para garantir a segurança, qualidade, produtividade e estabilidade dos processos. A Padronização tem por objetivo estabelecer métodos claros, especificos, compreendidos e principalmente consensados entre os turnos, facilitadores e operadores. Os principais benefícios do Trabalho Padronizado são: Produto com menor variabilidade e consolidação dos requisitos de cada posto de trabalho

Redução de Tempo de Setup - SMED
O SMED - Single Minute Exchange of Die é uma metodologia que tem por objetivo a redução dos tempos de preparação de máquinas e equipamentos, ou seja, redução dos Setups.
A razão mais comum para se terem tamanhos grandes de lotes em sistemas de produção são os tempos significativos de setup. Se são necessárias muitas horas para se trocar um molde de uma máquina para produzir um tipo diferente de peça, então faz sentido rodar lotes grandes entre as trocas. Tamanhos pequenos de lotes levariam a setups frequentes e comprometeriam a capacidade. Assim, a eliminação ou redução dos setups é uma precondição para alcançar tamanhos de lotes menores.
Nos Estados Unidos, os setups eram considerados uma necessidade, e os grandes lotes tinham o objetivo de manter um número mínimo de trocas. No Japão, a redução dos tempos de setup chegou ao ponto em que as trocas não influenciam na capacidade produtiva. Ohno descreveu setups na Toyota que foram reduzidos de 3 horas, em 1945, para 3 minutos, em 1971.
O segredo para uma abordagem genérica na redução dos setups é a distinção entre o setup interno e o setup externo. As operações de setup interno são aquelas tarefas que são executadas quando um máquina está parada, e as operações de setup externo são aquelas tarefas que podem ser executadas enquanto a máquina está funcionando.
Por exemplo, remover um molde é uma operação interna, mas reunir e preparar o ferramental para removê-lo é uma operação externa.
Segue abaixo quatro conceitos básicos para redução de setup:
1º Separar as operações de setup interno do externo.
2º Transformar ao máximo as tarefas de setup interno em externo.
3º Eliminar os processos de ajuste.
4º Eliminar o próprio setup.
Ferramentas do Lean Manufacturing

Kaizen
É um sistema de melhoria contínua no qual posturas de desperdício são eliminadas uma a uma, a um custo mínimo. É realizado por todos os funcionários, não por especialistas. Cada funcionário é responsável por contribuir para a melhoria contínua.

Kanban
O sistema Kanban trata-se de uma simbologia visual usada na indústria para registrar ações. A palavra que tem origem japonesa pode ser traduzida como “cartão visual”. No Brasil, o sistema Kaban é uma técnica bastante difundida, desde os anos 1980, quando começou a ser aplicada para a gestão de estoque e controle de fluxo de peças. O objetivo principal do sistema Kanban é permitir uma fina sintonia entre a gestão do estoque e a produção.
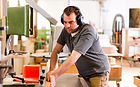
Poka-Yoke
O conceito de Poka-Yoke foi criado no início dos anos 60 por Shigeo Shingo, e o termo nada mais é que a combinação das palavras japonesas "poka" que significa erro não itencional, fruto da distração, e "yoke", que significa a prova de. Ou seja a tradução de Poka-Yoke é Aprova de Erro. O Poka-Yoke são métodos utilizados para eliminar ou detectar a ocorrência de erros durante um processo. Os dispositivos assumem as tarefas repetitivas ou ações que dependem da memória, liberando o tempo e mente dos operadores para que possam se dedicar à ações criativas ou que agregem valor ao processo.

5S

Formação de Lean Practitioneer em Lean Manufacturing
